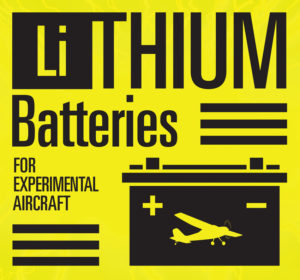
BY DICK SUNDERLAND
Lithium batteries are being used in increasing numbers in experimental aircraft because of their dramatically lighter weight, improved starting performance, and longer lives. They represent a new generation of batteries that are significantly different from lead-acid batteries. The differentiating peculiarities of lithium iron phosphate (LiFePO4 — abbreviated in this article as “Li” — is the chemical formulation most often used in experimental aircraft) can be explained, for example, by looking at my experience of changing out an Odyssey AGM lead-acid battery for an EarthX lithium battery on a Lycoming-powered RV-7.
BATTERIES
Batteries are characterized by three things. First is the total charge/energy of the battery expressed in ampere-hours (Ah). Next is the rate at which power can be withdrawn expressed in amperes (amps). Last is the ability of the battery to perform satisfactorily in its intended environment. Batteries in aircraft are used for two functions: starting the engine and sustaining electrical equipment usage. The distinction is very important because the two functions cannot be maximized within one battery. To date, aircraft batteries have been primarily starter batteries, with the expectation that an engine-driven charging system will take over after the start. The battery design is for a high burst of power for short periods of time. The power output of a starter battery is expressed in cranking amps. The opposite case is a sustainer battery, sometimes called a deepcycle battery. It is designed to operate for longer periods at much lower current. Today there is interest in the sustainer function as a backup for electronic ignitions and glass panels. For some applications it is reasonable to use batteries in “total loss” mode. That is using batteries for starting and/or sustaining loads and recharging on the ground. This avoids the cost, weight, and complexity of an in-aircraft charging system. Aircraft used for local flights, aerobatic planes, homebuilt helicopters, gliders, and motorgliders are some logical users. All batteries are concentrated reservoirs of energy and potentially dangerous with multiple failure modes. They must be cared for in accordance with the manufacturer’s instructions.
LITHIUM BATTERIES
Lithium batteries come in many chemical compositions with dramatically different characteristics. The details are the purview of chemists, engineers, and physicists. There is abundant material on the internet about them. Those who are interested can find a link to more in-depth information at: https://www.eaa.org/eaa/news-and-publications/eaa-magazines-and-publications/eaa-sport-aviation-magazine/this-months-extras
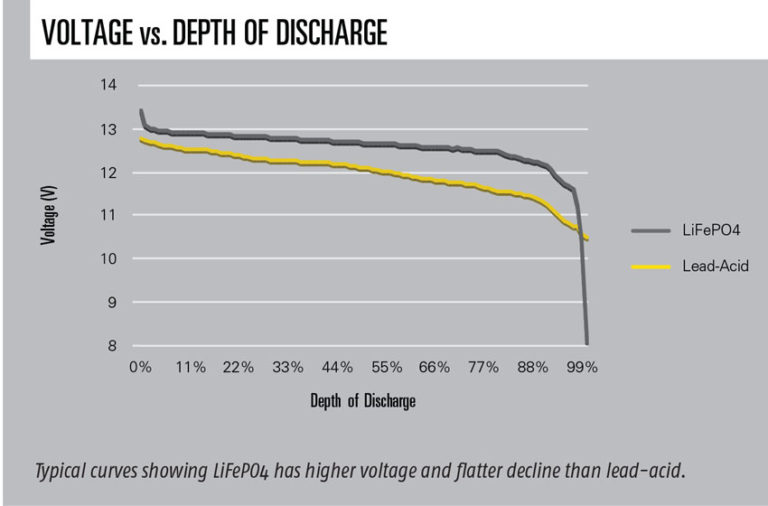
Lithium batteries show a relatively constant voltage during discharge, while lead acid shows sharper decreases, as shown in the accompanying graph. The nominal LiFePO4 battery voltage is 13.2 volts (four 3.3-volt cells) compared to 12.6 volts (six 2.1-volt cells) for lead-acid batteries. Upon cranking, a battery’s voltage goes down as the amps are drawn by the internal resistance of the battery, the circuitry, and the starting motor. Since a Li battery’s voltage is about 0.6 volts higher than a lead-acid one, and the internal battery resistance is smaller, the starter will have a higher end-state voltage during cranking. The starter will crank at roughly 5 percent higher speeds because starters are DC motors, the speed of which is controlled by voltage. For example, the Odyssey AGM lead-acid battery was getting 160 rpm, and I now get about 170 rpm with the Li battery. Reports of significantly higher starting speeds with Li batteries may simply be a function of replacing a worn-out battery with a fresh one. Li batteries have more discharge cycles before end of life. There are quotes of four to eight times the life of similar lead-acid batteries. As with all batteries, cycles are dependent on the depth of discharge (DOD) before recharging. If an engine starts quickly, the DOD will remain low, which promotes longer life. If the DOD is greater due to longer cranking or using the battery in sustainer mode, the life will be shorter. There is inconsistency among vendors as to how they measure and determine projected battery cycles/life. As with all batteries a Li battery’s capacity to provide cranking amps decreases over time. That can be accounted for by increasing the battery’s pulse cranking amps (PCA) or Ah size by 20 percent more than the minimum size for the task. Because of the significantly larger number of cycles with Li batteries, the amortized costs of Li batteries can be less than other technologies. In all batteries the usable Ah goes down exponentially as the rate of discharge goes up. The equation that demonstrates this is Peukert’s law. The exponent is a function of the batteries’ chemical compositions. Peukert’s law, plus a lead-acid starter battery’s lower DOD design, higher internal resistance, lower nominal voltage, and higher voltage decay all go into claims that only 30 percent of a lead-acid starter battery’s Ahs can be used for starting. This is the basis for Li manufacturers asserting that Li has three times the starting endurance of a lead-acid battery. Putting it another way, a Li battery could provide equivalent cranking time with a battery with one-third the lead-acid’s Ah. In the low amp sustaining mode, the usable Ah difference is small between Li and lead acid batteries of the same same Ah rating determined under the same load. Manufacturers’ charts list how long a specific load can be sustained.
LI TEMPERATURES CHARACTERISTICS
Like all battery types, Li batteries have temperature characteristics that users must be aware of. These characteristics are specific to the Li chemical formulation being used. Vendors will give a maximum and minimum temperature for the operating and storage environments for their batteries. Maximum temperature is particularly relevant for the RVs that have batteries mounted on the firewall. During flight there is heating due to convection and radiation from the engine and exhaust pipes. Upon shutdown there is no airflow so temperatures under the cowl will rise. The EarthX Li battery has a higher maximum operating temperature than the lead-acid Odyssey AGM battery it replaced (140°F versus 113°F). A battery is heated when cranking due to its internal resistance. Therefore rest periods are required if you are continuously cranking. One vendor recommends 30 seconds of rest following 10 seconds of cranking.
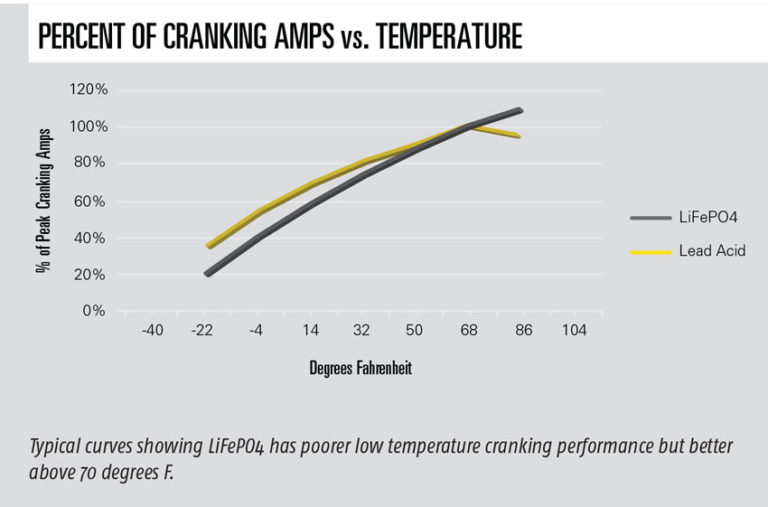
Li has a different curve for percent of cranking capacity available versus temperature compared to lead acid. This curve is typically higher than lead acid at higher temperatures but lower below freezing (see accompanying graph). Because I live in snow country, I opted for a one size larger Ah battery to achieve higher cranking amps at lower temperatures with a minor weight penalty. When starting at a very low temperature, one vendor suggests turning on the key for a few seconds; if the engine won’t turn over, wait 60 seconds to try again. Another vendor suggests turning on something that uses power, like landing lights, for a few minutes. In both cases, the current going through the battery warms it. Once it cranks, the battery will continue getting warmer. Minimum temperatures are also important because the battery accepts much lower charging currents at lower temperatures. Li batteries have low self-discharge rates, which is also a function of temperature. Self-discharge is the amount of power leaking in an unused battery per month (see accompanying graph).
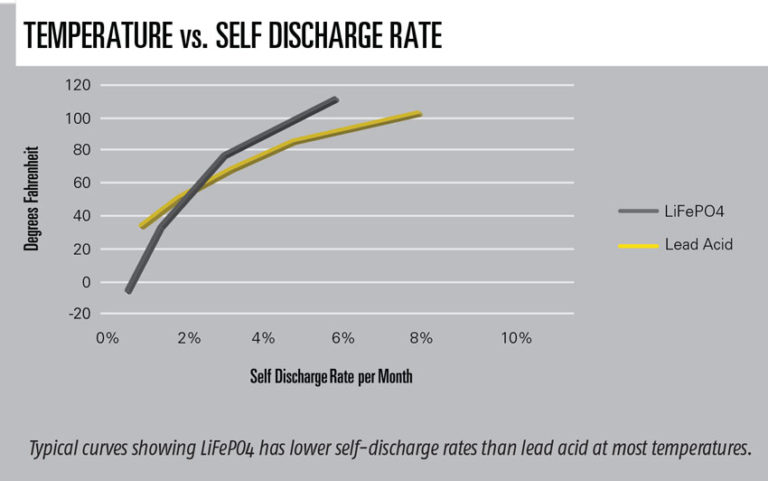
LITHIUM SAFETY
Lithium iron phosphate is considered the safest, least volatile, and most abuse-tolerant of the major lithium battery chemicals. Everyone is aware of the Boeing 787 and Samsung sagas. Much analysis and speculation is available on the web. Suffice it to say there are major differences in chemistries from the Li batteries now being used in light aircraft. The aircraft market has always been conservative about adopting new technologies. As a sign of the maturity and safety of Li batteries, there have been recent offerings for using Li batteries from major kit manufacturers like Sonex, Van’s, Zenith, and others. Their approval is a sign of their belief in the safety of Li batteries. The most common causes of failure in Li batteries are internal cell failure or overcharging. Internal cell failure usually results in a dead battery. Overcharging usually results in the production of heat and smoke, but not fire. Fire is extremely rare. Li batteries can be cooled and fire extinguished with water. Fumes are mainly carbon dioxide, vaporized electrolytes, ethylene or propylene, and other miscellaneous chemicals. The fumes, which smell like burnt plastic, are considered nontoxic in open environments but irritating to the lungs. It not is recommended that batteries be installed inside the fuselage unless it is in a vented box.
MANUFACTURING OF LI CELLS
Li batteries are made up of individual cells connected to achieve the desired voltages and amperages. The manufacturing of Li cells is high-tech and process sensitive. Cells can be in flat packs like Pop-Tarts or in round cylinders like dry-cell batteries. The cells are encapsulated in various configurations to fit existing battery boxes and terminal configurations. Assembly of cells into batteries is relatively inexpensive, so there are numerous assemblers of complete Li batteries worldwide.
POWER SPORTS INDUSTRY
The reason experimental aircraft owners have a wide variety of Li batteries to choose from is that we are benefiting from the power sports industry — the motorcycle, scooter, ATV, Jet Ski, snowmobile, race car, utility vehicle markets, etc. Those markets and users are weight sensitive, primarily need starter batteries, and are willing to pay for weight reduction. Very few of the power sports battery manufacturers refer to aircraft applications on their websites. It is speculated most Li providers think the aircraft niche is too small, too regulated, or too litigious. Most vendors offer some level of warranty, usually with use restrictions.
STARTER CIRCUITRY
The Li starter system schematic is the same as a lead-acid one. The whole circuit from the battery must be sized to handle the starting (inrush) surge, including the wiring, master solenoid, starting solenoid, and grounds. Different vendors use different metrics for quantifying the ability to crank an engine. There seems to be general dissatisfaction with the applicability of the traditional automotive measure of cold cranking amps (CCA). Most Li battery vendors supply both CCA and a version of PCA, which is generally based on five seconds of cranking at 77 °F. For example, a typical Lycoming 360 starter can draw 300 amps while cranking, but the inrush current can be more than double that value. A good rule of thumb is to select a battery with a PCA of double the starter rating.
CHARGING CIRCUITRY
The charging system schematics are the same as lead acid. Again, the whole system must be examined to see if it is robust enough to cope with the higher charging amps that Li batteries accept. My aircraft showed more than double the recharging rate after starting once I switched to the EarthX battery. Generators can be used to charge Li batteries. Since many generator installations are old, critical examination of all system components must be done to ensure their ability to handle higher current levels than those experienced with a lead-acid battery. The alternator or generator must be sized so that its failure mode will not overcharge the battery. EarthX has an excellent flowchart on its website about decisions on the charging circuit, including comments on Rotax engines.
VOLTAGE REGULATION
A standard practice in certificated aircraft is to use external voltage regulators with overvoltage protection, usually known as a “crowbar” circuit. Many experimentals have used alternators with internal voltage regulators that may or may not have a crowbar circuit. Li batteries require a charging voltage of 14.0 to 14.6 volts. Since an internal regulator is not adjustable you must determine if your alternator outputs are in the voltage window. EarthX requires crowbar overvoltage protection.
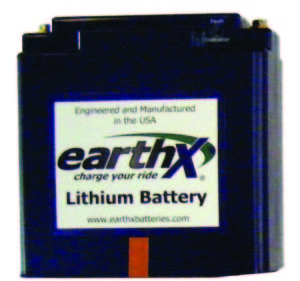
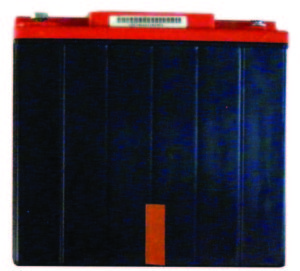
Li battery (left) compared to a lead acid (right) of equivalent Ah. Note the Li battery is packaged in a larger volume than necessary. That is often done to fit standard battery boxes and to save mold costs.
BATTERY MANAGEMENT SYSTEMS
A critical choice you must make is whether or not to purchase from a vendor that has a battery management system (BMS). A BMS is a circuit board internal to the battery. It protects against over discharge, overcharging, internal shorts, cell mbalance, and over cranking/thermal damage. These BMS functions supplement but do not take the place of a voltage regulator. Be aware that at least one vendor calls its battery charger a BMS. Most Li batteries have some form of internal cell-balancing circuitry. However that is not considered to be a BMS. At the time of writing EarthX was the only vendor in the 12-volt space that has a comprehensive BMS. It is possible to use Li batteries without a BMS, but you must manage the risks yourself. A BMS is a significant addition to the price of the battery. The gain is safety, robustness, and protection of other electrical equipment. A certified Li battery requires a BMS. A battery used in an E-AB aircraft does not have to meet a technical standard order (TSO). However, prudence would suggest that the TSO requirements should be considered to be best practices. The TSO requirements for Li batteries are found in RTCA publication DO-347.
BATTERY MAINTENANCE
Li batteries have very different care needs than lead acid. They have vendor-specific requirements for chargers, charging profile, trickle charging, and topping off. Many conventional lead-acid chargers are unsuitable because they use a pulse charging feature known as “desulfating.” Others are unsuitable because the maintenance voltage level is too low (below 13.4 volts). An aircraft with a partially depleted Li battery can be jump started from a fully charged lead-acid battery but only from one of the same or lower Ah rating. Li batteries cannot be revived if totally discharged even one time. This means either very careful management or the use of a BMS for cutoff before total discharge.
STATUS OF YOUR CURRENT BATTERY
You should consider the health and confidence you have in your current battery to perform your mission. If your current battery has remaining life and your mission does not require the performance attributes of Li, you might not want to switch now. However, when you hit a battery replacement situation you should reconsider Li. As with most high-tech products, Li is evolving. By waiting, you may have the choice of cheaper or better batteries in the future.
WEIGHT AND BALANCE
Your weight savings, including attachment systems, are dependent on your starting point. For example, going from a flooded lead-acid battery at 24 pounds to a Li at 4 pounds, you could save 20 pounds. But if you have an Odyssey AGM battery at 15 pounds, you will save only 11 pounds. You must consider what difference a lighter battery makes in your aircraft’s balance. Designers consider battery placement based on the battery weight/sizing they think appropriate and the technology of the day. Switching to a lighter battery and battery holder may impact or create new CG issues.
AFTER INSTALLATION
After installing a Li battery there are several important tasks to do. Your weight and balance data should be updated, including limiting cases. For an electrically dependent aircraft you should recalculate and test your emergency power endurance. Your gauges or EFIS should be adjusted or re-marked to show new operating parameters. If the changes were extensive, then you should consider re-entering Phase I flight testing. At condition inspection time you should record the battery’s voltage and do a cranking amps test to show aging trends. Finally, update your pilot’s operating handbook for any changes in emergency procedures. Li batteries can decrease weight, improve starting performance, and outlast lead-acid batteries. The benefits depend upon understanding their pluses and minuses, your current situation, and your missions.
Dick Sunderland, EAA 250386, has been flying since the 1980s and has earned his airline transport and multiengine ratings. He’s an airplane geek, a super fan of EAA AirVenture Oshkosh, and built an RV-7, which he flies out of Granby-Grand County Airport. Dick can be reached at pilot4857@q.com. This article is being republished with the permission of EAA Magazine and Dick Sunderland. Originally printed on page 88-92 of SportAviation Magazine – March 2018 Edition.